Process FLow
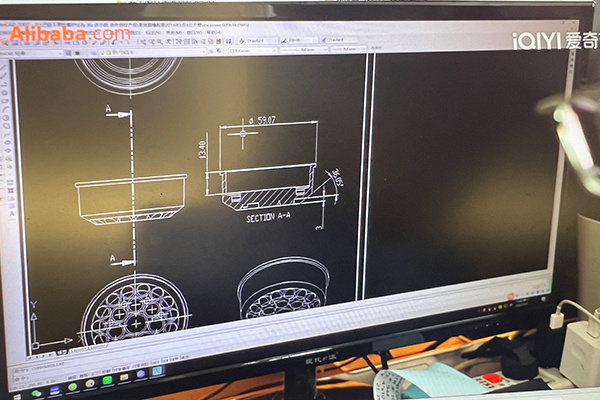
01
Mould Design
The mold design engineer designs the mold structure based on customer requirements, product drawings, and design requirements, and issues the mold structure diagram. Then submit it to the mold department manager for review and determine the plan.
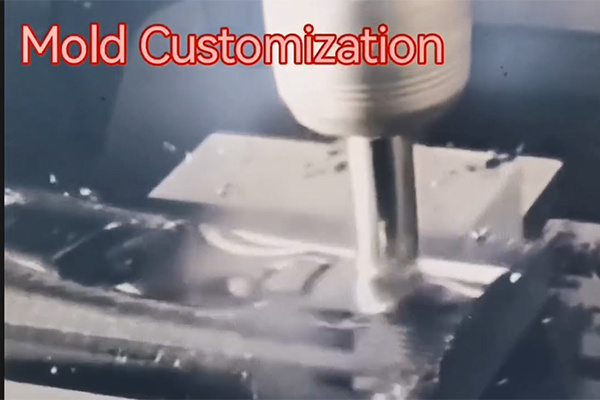
02
Mould Making
The mold production process is as follows:Material preparation→Mold base processing→Mold core processing→Electrode processing→Mold parts processing→Inspect→assemble→Flying mold→Test mold.
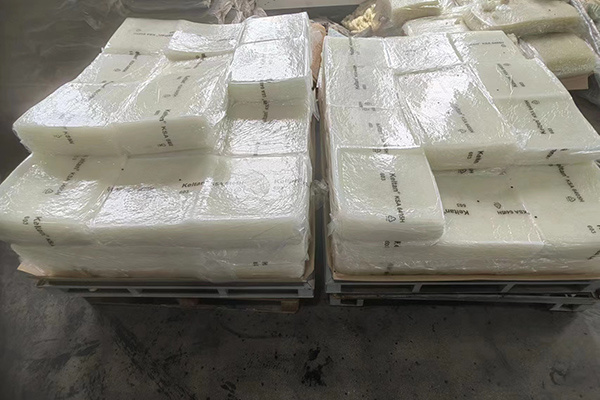
03
Raw Material IQC
Raw material IQC: Refers to the quality confirmation and inspection of purchased raw materials, components, or products. When the supplier delivers raw materials or components, the product is inspected through sampling. And finally make a judgment on whether the batch of products is to be received or returned or exchanged.
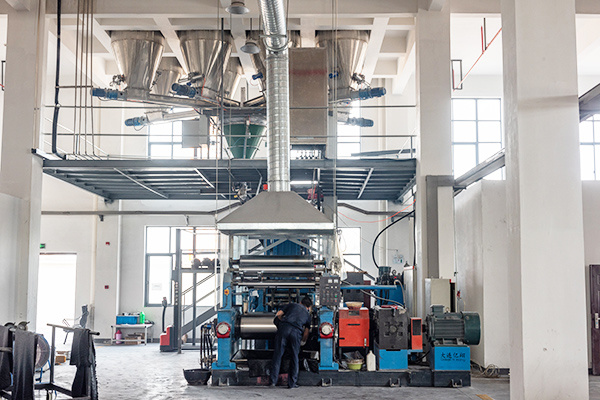
04
Weighing Of Ingredients
Auxiliary material weighing is the process of applying an automatic batching control system to dynamically weigh and control auxiliary materials. According to the requirements of the process flow and the predetermined formula, various auxiliary materials are added to the weighing hopper according to the corresponding proportion of weight values for weighing.
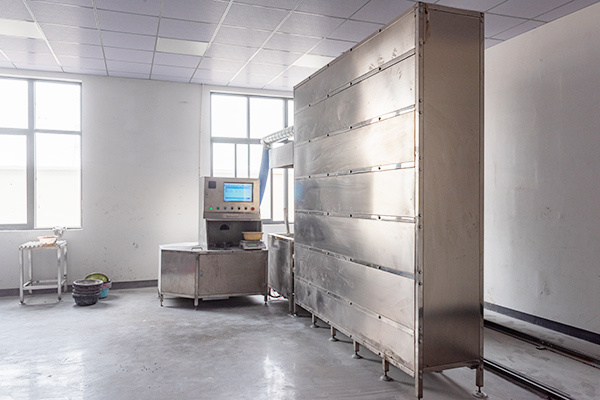
05
All Material Mixing
All material mixing is the process of mixing the raw rubber after molding with the compounding agent and placing it in a rubber mixer. Through mechanical mixing, the compounding agent is completely and evenly dispersed in the raw rubber. Mixing is an important process in the production of rubber products. The rubber material obtained after mixing is called blended rubber, which is a semi-finished material used to manufacture various rubber products.
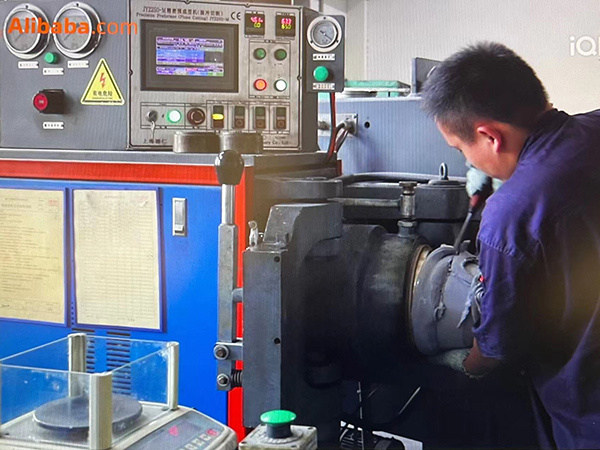
06
Extrusion Material
Squeezing refers to the production of various hardness and shape rubber preforms through rubber pre forming machine processing. he processed rubber preform has high precision and no bubbles, making it suitable for producing corresponding rubber products.
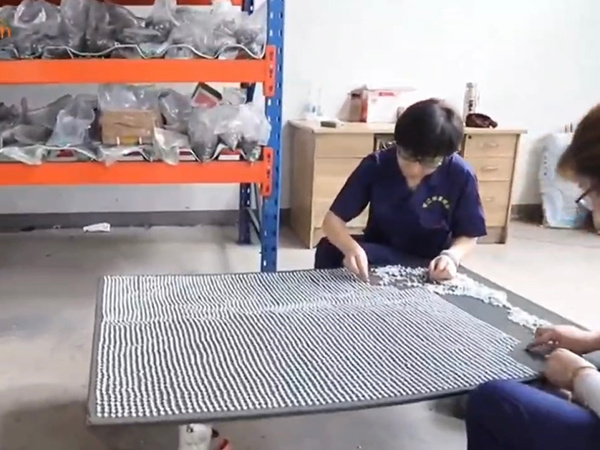
07
Iron Parts Spraying
The spraying process for iron parts is as follows: Iron parts cleaning→sand blast→Phosphating→Spray primer adhesive→dry→Spraying surface coating adhesive→dry.
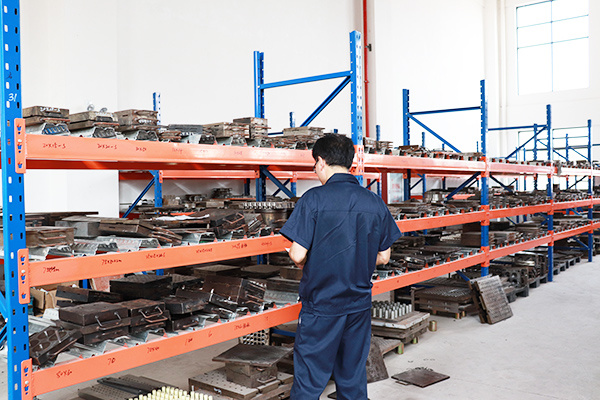
08
Mold Preparation
Mold preparation refers to checking the mold cavity for impurities, oil stains, or rust before vulcanization production. After cleaning the mold cavity, check whether the interior of the mold cavity surface is intact. Only qualified molds can be used for molding production.
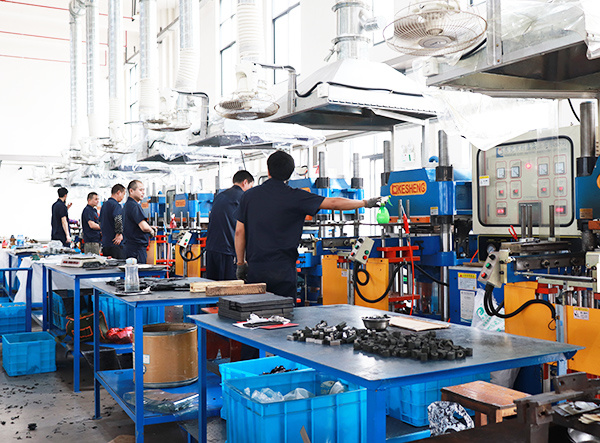
09
Vulcanizing
Vulcanization is the final process in the manufacturing process of rubber products . Load the mixed rubber formed by the molding machine into the mold, and then place the mold in a flat vulcanizing machine. Set the required pressure, temperature, and time to allow the rubber material to undergo vulcanization reaction, thereby forming a stable chemical structure.
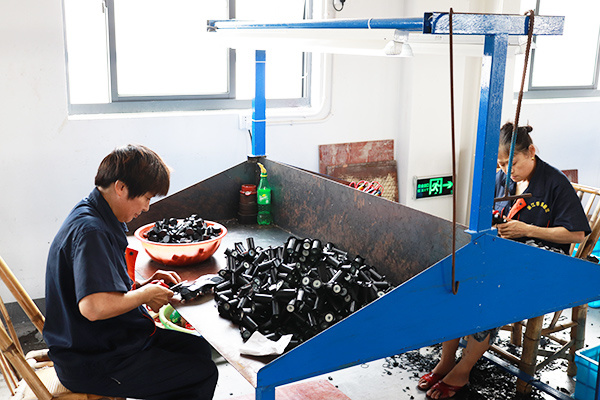
10
Trimming
Edge trimming mainly involves removing the rubber edges after vulcanization molding of rubber products. It includes using a punch to cut the adhesive edge, and using scissors, scrapers, and other tools to remove the adhesive edge. The purpose is to ensure that the rubber finished product meets the technical requirements required by the customer.
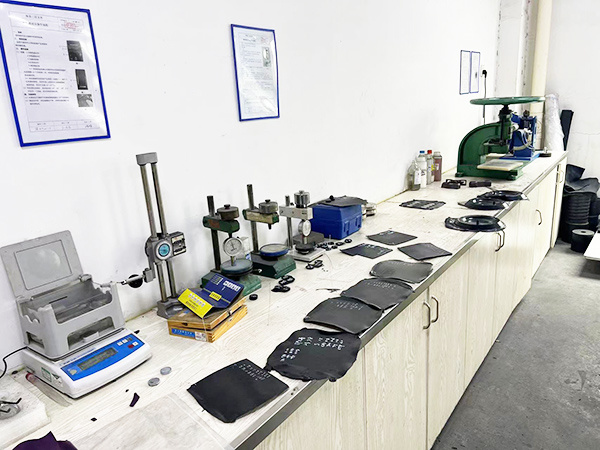
11
QC
Quality inspection is to ensure that rubber products comply with relevant standards and regulations. The content includes multiple aspects such as appearance quality, size, hardness, tensile strength, elongation at break, tensile deformation, vulcanization time, etc. If the product does not meet the relevant requirements, it is necessary to adjust the production equipment or process in a timely manner.
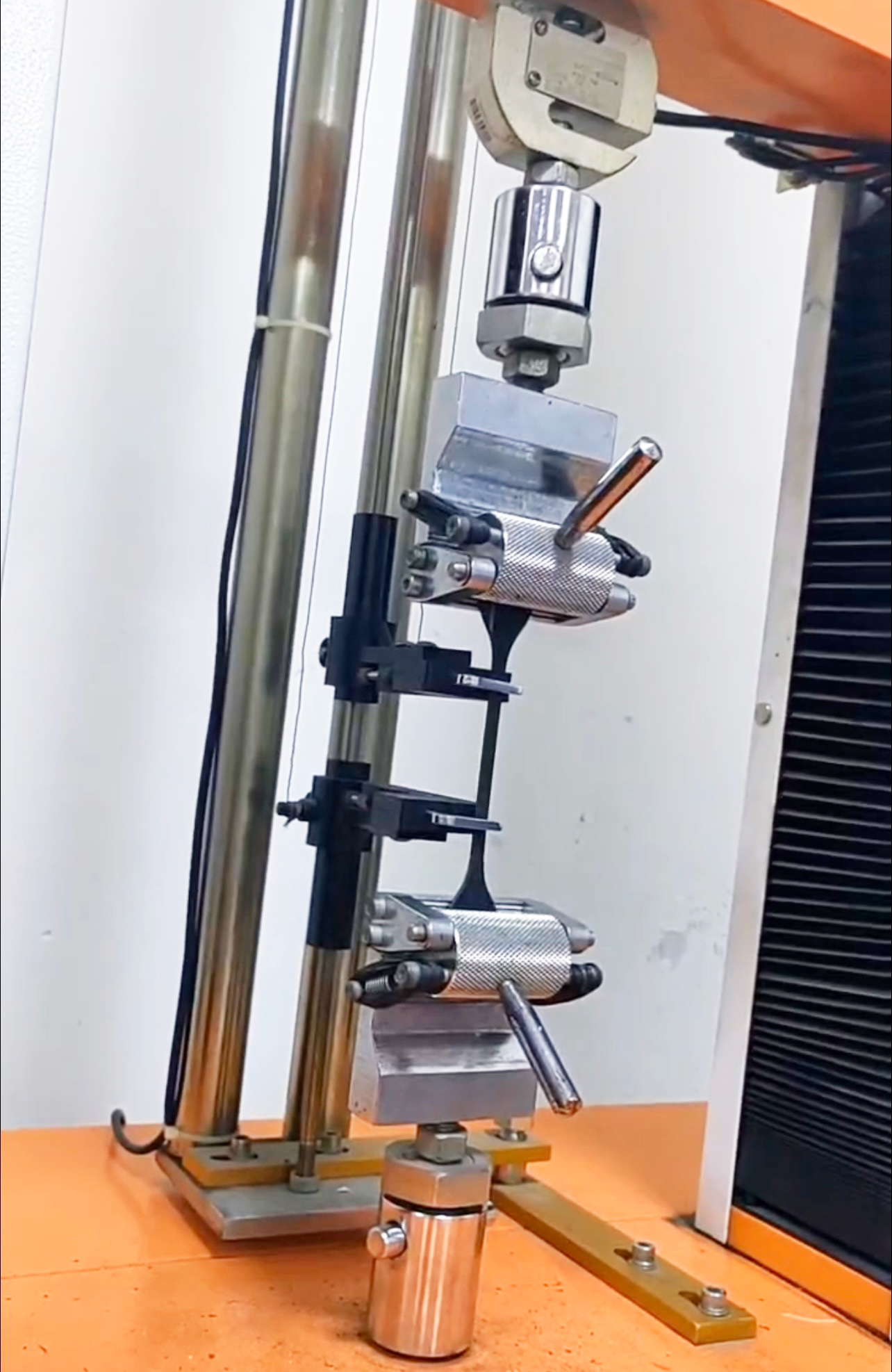
12
Final Inspection
Final inspection is a comprehensive inspection and testing of the finished product after completion. Its purpose is to prevent unqualified products from flowing into the hands of users, avoid causing losses to users, and also to protect the reputation of the enterprise.
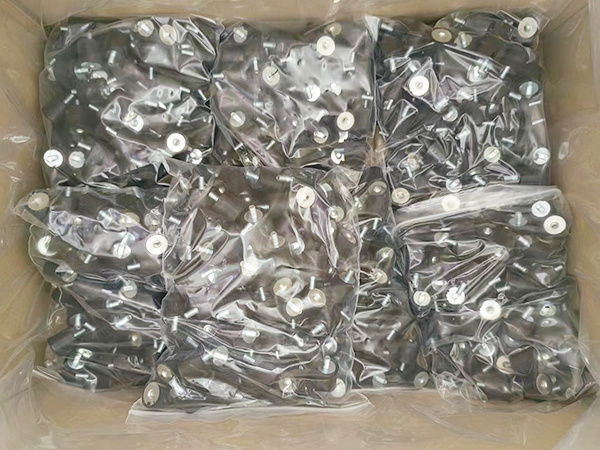
13
Inner Packing
The main purpose of inner packaging is to ensure the sealing of the packaging. Because rubber products are susceptible to moisture, oxidation, or other pollutants, choose sealed plastic bags with good sealing properties for packaging. To better protect the quality of rubber.
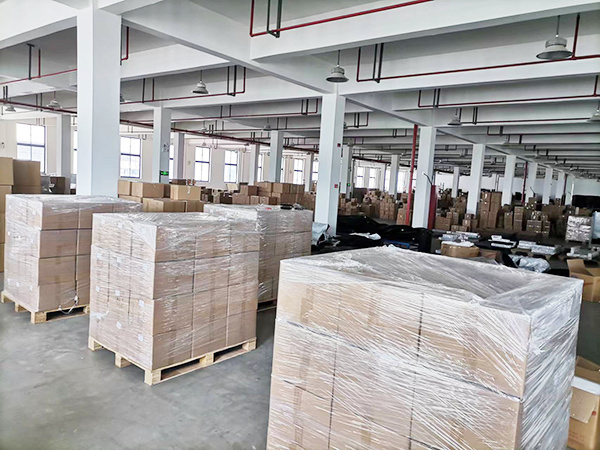
14
Outer Packing
The outer packaging is mainly used to prevent external factors from damaging. Carton is one of the most widely used materials in the packaging of small and medium-sized rubber products. It can protect rubber from pollution and external forces, and is suitable for small and medium-sized transportation.
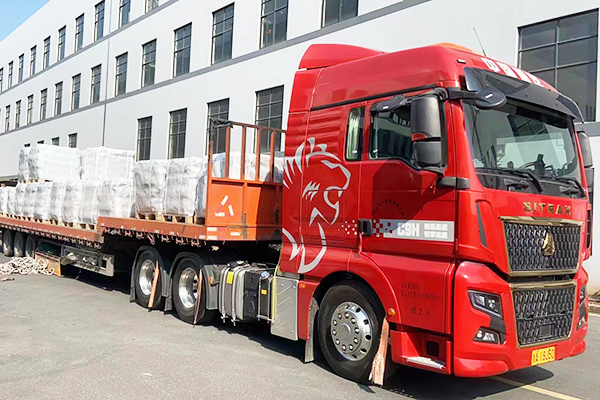
15
Shipment
Shipping is the last step before the product arrives at the customer. The warehouse arranges professional warehousing personnel for shipment. At the same time, we have long-term and good cooperation with major logistics companies to ensure the fast and safe delivery of goods to customers.